Cinque sfide in produzione che puoi vincere adottando un sistema di Advanced Planning & Scheduling
Adottare un sistema di pianificazione e schedulazione della produzione non significa solo digitalizzare un processo fondamentale per il successo complessivo dell’intera produzione, ma anche implementare le giuste strategie di ottimizzazione essenziali per rispondere istantaneamente ad eventuali criticità e interruzioni del piano di produzione.
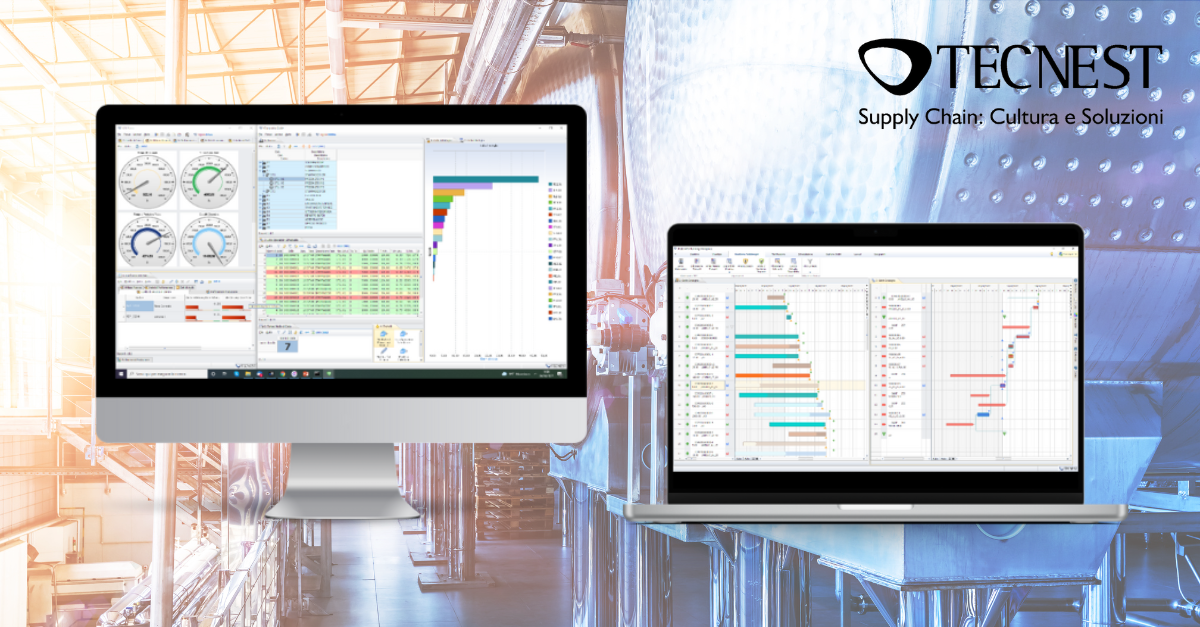
Gran parte delle generali criticità riscontrate in fabbrica durante la fase produttiva derivano infatti da un’inadeguata pianificazione delle commesse. Questo spesso porta a errori nella datazione delle consegne o inefficienze nel piano produttivo, al mancato rispetto dei vincoli, al sottoutilizzo delle capacità delle macchine, complicazioni nel setup delle macchine e a ritardi nella gestione delle criticità.
Ecco quindi perché un sistema automatico di pianificazione e schedulazione consente di considerare tutti gli elementi critici che altrimenti, con l’impiego di strumenti manuali, verrebbero trascurati nello sviluppo del piano di produzione.
Con l’implementazione di un sistema APS (Advanced Planning and Scheduling) è possibile affrontare con successo cinque sfide principali nell’ambito della produzione:
-
La gestione dell’approvvigionamento.
Attraverso il Material Requirements Planning, l’APS permette di garantire il corretto approvvigionamento dei materiali, assicurando che i fabbisogni del piano di produzione siano soddisfatti in linea con le previsioni e gli ordini di vendita. Allo stesso tempo, mantiene una scorta adeguata di magazzino per evitare situazioni di stock-out, preservando così la disponibilità di prodotti a magazzino.
-
L’affidabilità delle date di consegna.
Rispettare le date di consegna promesse al cliente rappresenta un indicatore di qualità cruciale nel servizio offerto al cliente. Per garantire ciò, diventa essenziale attivare un processo di datazione automatica che consideri tutte le variabili del processo produttivo, come i carichi di lavoro e la disponibilità dei materiali.
-
Ad ogni pianificazione corrisponde una “reazione”.
In un mercato caratterizzato dalle continue fluttuazioni, è fondamentale considerare l’imprevisto come parte integrande della pianificazione stessa. Ciò significa non solo individuare potenziali criticità, ma soprattutto essere in grado di reagirvi tempestivamente, valutando alternative in modo da ottenere i migliori risultati nel medio-lungo periodo.
-
La pianificazione chiama, la schedulazione risponde.
Dopo aver generato e pianificato le attività, è necessario allocarle nel tempo e nello spazio. La schedulazione automatica consente di rispondere a domande cruciali come quando eseguire una determinata attività e su quale risorsa. Questo approccio permette quindi di evitare problemi quale la mancanza di manodopera adeguata, conflitti di disponibilità delle risorse e conseguenti ritardi.
-
Reattività potenziata dal sequenziatore di reparto.
Il sequenziatore di reparto rappresenta uno strumento supplementare per supportare l’operatività della fabbrica. È utile sia che si tratti di rispondere a situazioni critiche impreviste che richiedono interventi diretti in reparto, sia come alternativa alla schedulazione automatica. Il sequenziamento manuale costituisce un valido strumento per generare o rigenerare la sequenza di lavorazioni, alimentando così l’attività produttiva della fabbrica.
Possiamo quindi concludere che l’adozione di un sistema APS consente di:
-
ottimizzare l’approvvigionamento,
-
garantire date di consegna affidabili,
-
affrontare in modo integrato le sfide della pianificazione,
-
sincronizzare pianificazione e schedulazione,
-
migliorare la reattività tramite il sequenziamento in reparto.
Lo scopo finale è contribuire a migliorare l’efficienza, la flessibilità e la capacità di adattamento della fabbrica nell’ambito della produzione.