Predictive Advanced Analytics: i vantaggi di un approccio predittivo al servizio della competitività della fabbrica
Creare una vera e propria catena del dato di processo, dagli impianti produttivi ai sistemi MOM, permette di stravolgere l’approccio attuale orientato alla “reattività” rispetto ad eventi che si dovranno ancora verificare, ad un approccio “predittivo” in grado di anticipare criticità e derive produttive fornendo, in tempo reale, importantissime informazioni di processo. Grazie alla soluzione FLEX e IIOTCore di Tecnest, oggi siamo in grado di entrare nel “DNA” di ogni produzione trasformando i dati in asset strategici.
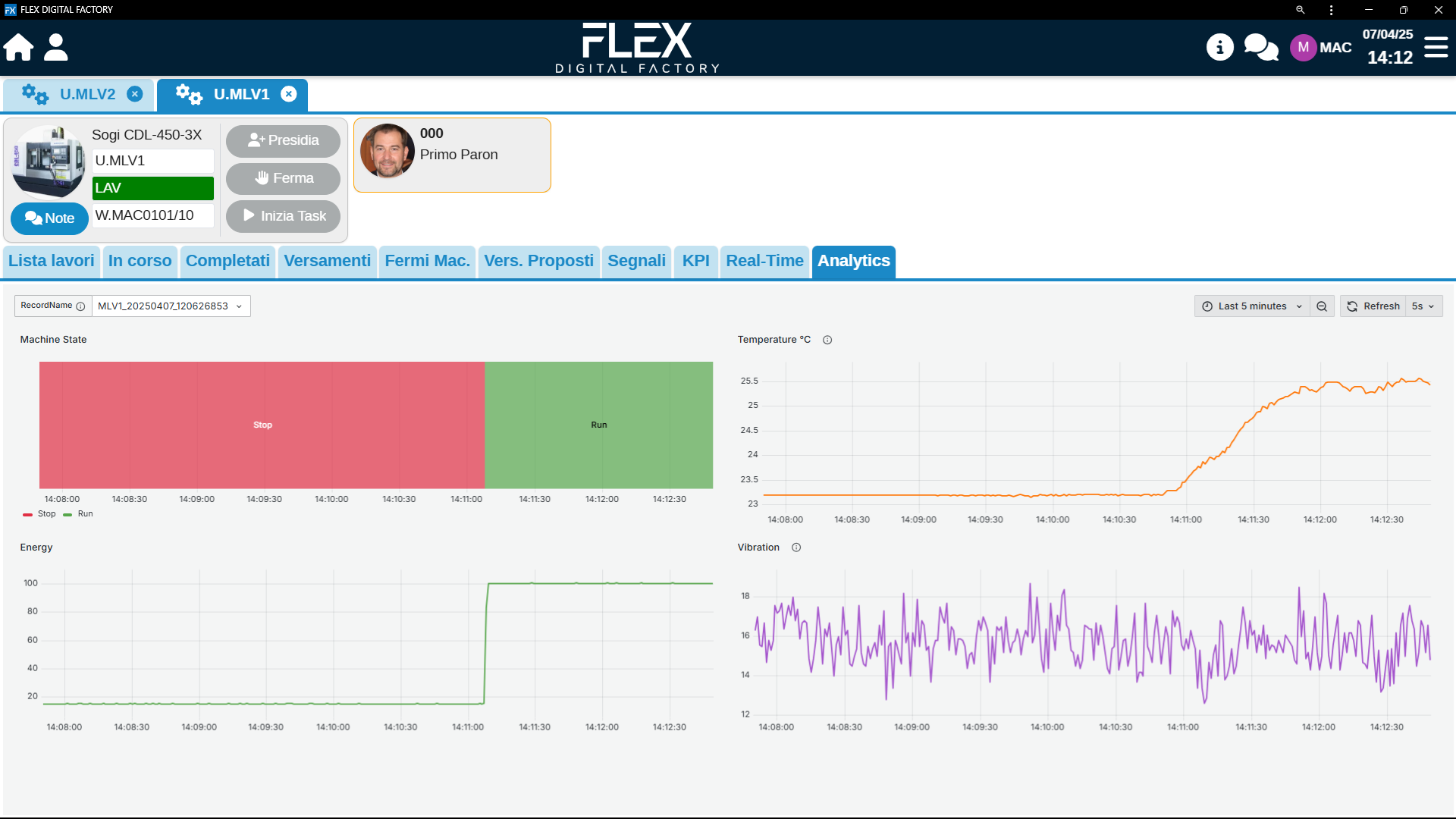
Nel contesto industriale moderno, i dati rappresentano una risorsa strategica che, se raccolta e analizzata correttamente, consente alle aziende di trasformare le proprie operazioni da reattive a predittive. Grazie alla sinergia tra i dispositivi sensoristici per la raccolta dati, i devices IIOT e la soluzione MOM, è possibile oggi avere in qualsiasi momento un’istantanea dell’andamento delle proprie macchine produttive, avendo quindi evidenza di eventuali criticità lungo la linea in termini di performance e consumi.
Le Predictive Advanced Analytics rappresentano quindi un elemento chiave per una strategia volta ad una conoscenza ancora più approfondita dei propri processi capaci di guardare al passato ed al presente anticipando il futuro.
Fermarsi ad un’analisi descrittiva, ovvero all’osservazione di ciò che è accaduto in passato è oramai un approccio superato. Nell’ecosistema della fabbrica intelligente le Advanced Analytics permettono di fornire risposte a domande cruciali:
-
Cosa succederà? (previsione di guasti, ritardi)
-
Perché succederà? (correlazioni tra dati di produzione e variabili di processo)
-
Come possiamo intervenire? (strategie ottimali per minimizzare l’impatto di anomalie e migliorare le performance)
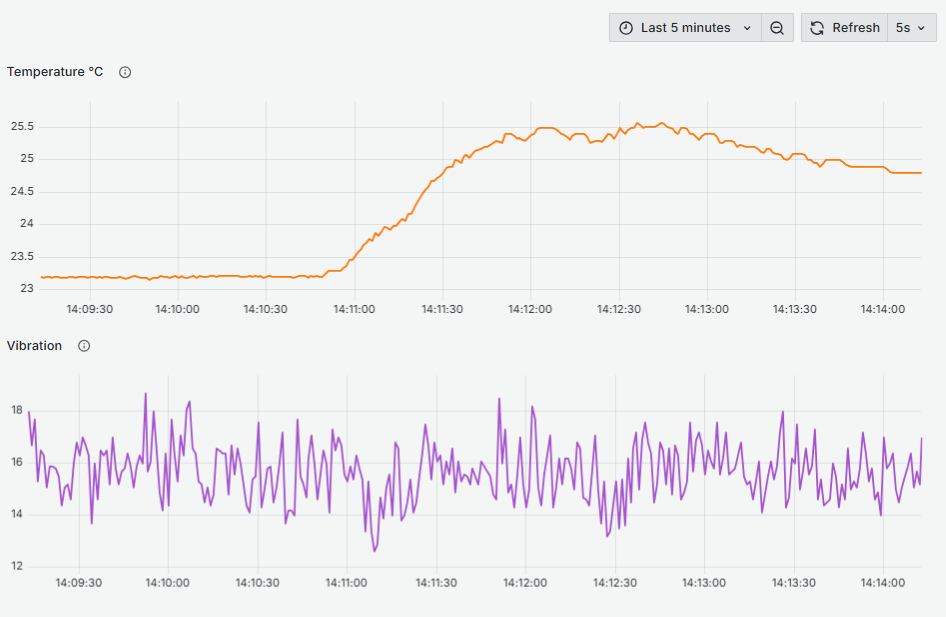
I vantaggi per l’intera produzione
-
Maggiore visibilità sulle operazioni: avere dati di dettaglio accurati in tempo reale permette di monitorare l’andamento della produzione, individuare inefficienze e ridurre sprechi.
-
Riconoscere pattern e trend: analizzando i dati storici inerenti a KPI telemetrici come temperatura, vibrazione, pressione e consumi energetici, è possibile identificare ed analizzare schemi ricorrenti e prevedere criticità prima che si verifichino, migliorando la continuità produttiva.
-
Cost Controlling e sostenibilità: conoscere nel dettaglio il consumo energetico di ogni impianto è oggi fondamentale per garantire una politica produttiva volta al risparmio energetico sia in termini di sostenibilità, sia in termini di contenimento costi generali. Avendo evidenza quindi del consumo, sarà possibile ri-orientare i propri processi produttivi verso una maggior efficienza.
-
Manutenzione predittiva: grazie all’analisi avanzata, le aziende possono prevedere il degrado delle attrezzature e intervenire prima che si verifichino guasti, riducendo i tempi di fermo macchina e i costi di manutenzione.
-
Miglioramento della qualità: il monitoraggio continuo dei parametri di processo permette di ridurre difetti e scarti, aumentando l’affidabilità del prodotto finale.
RICHIEDICI UNA DEMO