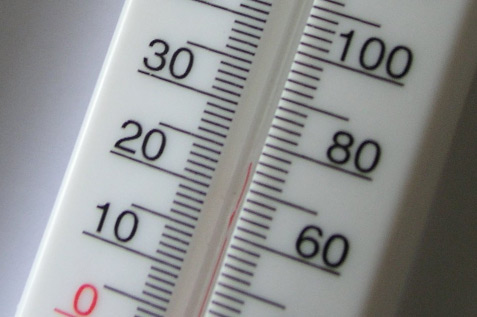
Varem is a company located in Limena (PD) specialized for more than 40 years in the production of expansion vessels for boilers, for thermal and solar thermal systems.
The Company chose Tecnest's FLEX for Industry 4.0 system including MES modules for data collection and factory monitoring, TQM (quality management), TPM (maintenance management), WMS (warehouse management), IIoT (Industrial Internet of Things ) to ensure complete production and logistic monitoring with increasingly efficient performance.
The project involves interfacing with the existing ERP system and with the production machines, in particular through the bi-directional interconnection required by the national Industry 4.0 plan.
Varem è un'azienda di Limena (PD) specializzata da più di 40 anni nella produzione di vasi di espansione per caldaie, per impianti termici e solari termici.
La Direzione di Varem si è posta l'obiettivo di digitalizzare completamente la fabbrica per un’organizzazione avanzata real time dei processi produttivi.
Ha scelto quindi il sistema FLEX for Industry 4.0 di Tecnest comprensivo dei moduli MES per la raccolta dati e monitoraggio in fabbrica, TQM (gestione della qualità), TPM (gestione della manutenzione), WMS (gestione magazzini), IIoT (Industrial Internet of Things) per garantire un completo monitoraggio produttivo e logistico con performance sempre più efficienti. Il progetto prevede l’interfacciamento con il sistema ERP esistente e con le macchine di produzione, in particolare attraverso l’interconnessione bidirezionale richiesta dal piano nazionale Industria 4.0.
Acqua Brevetti S.r.l. è una realtà produttiva focalizzata sulla progettazione e realizzazione di apparecchiature per il trattamento dell’acqua per applicazioni civili ed industriali.
L'azienda ha scelto Tecnest e FLEX MES per un progetto di raccolta e monitoraggio attività di produzione, comprensivo di interconnessione alle macchine operatrici conforme alla normativa Industry 4.0, per lo stabilimento di Mestrino (PD).
Un progetto di schedulazione della produzione e MES realizzato per migliorare la datazione degli ordini e ottimizzare il piano schedulato, ridurre i tempi di attrezzaggio delle macchine, reagire in tempo reale sui cambiamenti nell’area produttiva, migliorare l’efficienza dello stabilimento al cuore del processo produttivo di una delle più importanti aziende italiane nel settore della refrigerazione.
Rivacold è un'azienda specializzata nella costruzione di impianti e gruppi per la refrigerazione che si dividono in 3 principali linee di prodotto:
L'ampia gamma di prodotti si sviluppa in versioni standard e a disegno del cliente in diverse applicazioni dedicate ai seguenti mercati Ho.Re.Ca., vending GDO, agro-alimentare, medicale e farmaceutico.
Nell’ambito del processo produttivo di Rivacold costituisce un nodo centrale lo stabilimento chiamato “Rivacold 5”, dedicato alla produzione di pacchi batteria e componenti per le altre divisioni dell’azienda.
Tale stabilimento si trova al cuore del processo produttivo di Rivacold e risulta critico in particolare a causa delle macchine presenti (presse, saldatrici e mandrinatrici) che possono richiedere fino a un’ora di tempo per l’attrezzaggio.
A causa di questi lunghi tempi di attrezzaggio, lo stabilimento Rivacold 5 rappresentava un collo di bottiglia per l’intero processo produttivo. Lo stabilimento è suddiviso in due reparti, in uno di questi la fase che determina il ritmo produttivo e dà il battito alla produzione, è quella di pressatura, nell’altro la fase critica è la mandrinatura.
Inoltre il processo di programmazione e schedulazione della produzione gestito da Rivacold tramite l’MRP del gestionale AS400 ed Excel, presentava alcuni limiti. In particolare si riscontravano difficoltà nel definire una data precisa di consegna al cliente e nel fare valutazioni precise sul carico nel medio e nel breve periodo. Gli ordini stampati e rilasciati venivano sequenziati ed assegnati alle risorse dai capireparto con logiche di ottimizzazione delle macchine basate sull’esperienza, senza una visione globale degli ordini in essere.
Infine il processo di ripianificazione in caso di urgenze risultava molto dispendioso e non si aveva una visione precisa dello stato di avanzamento dei vari ordini.
Sulla base di queste considerazioni il management di Rivacold ha deciso di implementare una soluzione APS e MES con il supporto di Tecnest per migliorare i processi di schedulazione e avanzamento della produzione.
Con il progetto affidato a Tecnest, Rivacold si era posta l’obiettivo di migliorare il processo di datazione degli ordini e ottimizzare il piano schedulato al fine di rispettare il piano di consegna e minimizzare gli attrezzaggi.
L’introduzione di un sistema di Advanced Planning & Scheduling doveva aiutare ad automatizzare il processo di pianificazione di medio e lungo periodo, minimizzando le attività di modifica manuale del piano rilasciato e dare la possibilità di modificare il piano effettuando valutazioni simulative “what-if”.
Un’altra esigenza era quella di poter individuare per tempo le criticità produttive, in termini di mancato rispetto delle date di consegna al cliente, di variazione delle forniture (esterne o interne alla Rivacold) che costituiscono un vincolo per l’avvio delle attività e di variazione delle giacenze.
In reparto era inoltre importante avere a disposizione il piano schedulato in tempo reale, visualizzare disegni tecnici direttamente a bordo macchina, raccogliere i tempi consuntivati sulle risorse macchina e manodopera al fine di verificare l’efficienza e analizzare la bontà dei tempi preventivi e avere una visualizzazione in tempi rapidi dello stato di avanzamento dei singoli ordini produttivi
In una prima fase di progetto è stata fatta un’analisi dei processi di Rivacold 5, in particolare lo studio dell’albero delle risorse (macchine, gruppi macchina, centri di lavoro), la revisione dei cicliper fornire allo schedulatore dati che replicassero in modo fedele il processo produttivo e la formalizzazione dei vincoli di processo (matrici di set-up).
Nel gestire il processo di schedulazione in Rivacold 5 ci si è concentrati sull’ottimizzazione delle fasi critiche che determinano il ritmo produttivo nei due diversi reparti. In un caso la fase critica è quella di pressatura, nell’altro è la fase di mandrinatura.
[...]
TECNEST S.r.l. - Reg. Imprese di Udine, C.F. e P.IVA 01534200306 - Iscr. C.C.I.A.A. - Udine R.E.A. 179349 - Cap. Soc. 31.200,00 Euro i.v.
© Multiways 2013 / Privacy policyCookie policy