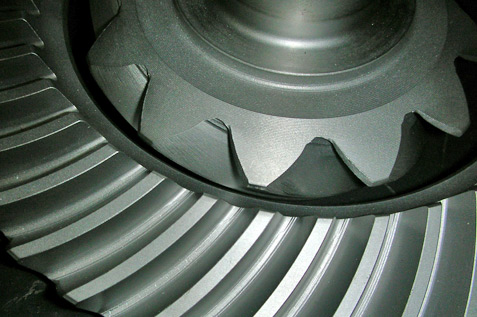
Innovation Mould, azienda veneta specializzata nella progettazione e produzione di stampi per la produzione di elementi a struttura complessa, ha cominciato la sua partnership con Tecnest scegliendo FLEX-APs per il proprio stabilimento produttivo di Treviso.
Dall’ufficio tecnico alla produzione risorse, progetti e commesse sono ora interamente pianificati con grande beneficio per quanto riguarda l’organizzazione delle risorse umane, l’evidenza di situazioni di criticità e sovraccarico in real-time sia del comparto di sviluppo sia del comparto produttivo ed un conseguente miglioramento effettivo delle tempistiche di consegna che diventano più esatte.
EAS elettronica è un’azienda di Vicenza leader nella subfornitura elettronica, che si occupa dell’assemblaggio di schede elettroniche manuale e Smd.
EAS fornisce un servizio omnicomprensivo ai propri clienti, che va dalla progettazione e ingegnerizzazione di apparecchiature elettroniche industriali, alla realizzazione di prototipi, master e campionatura per l’elettronica, collaudi burn-in a processi complessi e strettamente correlati.
Per il proprio stabilimento produttivo di Schio, in un'ottica di gestione della produzione, EAS ha scelto la suite FLEX- APS e MES.
Grazie allo strumento grafico e interattivo di FLEX, l’azienda sarà in grado di dare nuovo slancio alla produzione migliorando performance e tempistiche grazie al supporto fornito dal software, nelle attività di individuazione della data di consegna del prodotto finito concordata con i clienti, nella pianificazione e sequenziazione della produzione e nella raccolta e monitoraggio delle attività di produzione.
Una soluzione di pianificazione della produzione che ha permesso di allineare i tre layer organizzativi dell'azienda, Supply Chain, Commercial Offices e Manufacturing e di gestire realtà produttive e organizzative molto diverse a livello globale, migliorando l’On-time delivery, i volumi di produzione e riducendo i costi.
Trelleborg Wheel Systems è leader mondiale nella fornitura di pneumatici e ruote complete per macchine agricole e forestali, per carrelli elevatori e altre attrezzature per la movimentazione di materiali, per veicoli da costruzione, motocicli, biciclette e altri segmenti speciali.
Trelleborg Wheel Systems ha 15 stabilimenti industriali e più di 50 centri distributivi in tutto il mondo; è una divisione del Gruppo Trelleborg, leader mondiale nello sviluppo di soluzioni polimeriche avanzate. Il Gruppo ha un fatturato annuale di circa 3,32 miliardi di euro e attività in circa 50 Paesi.
Per mantenere la propria competitività e garantire il miglior servizio al cliente finale, la Direzione di Trelleborg Wheel System ha deciso di affidare a Tecnest un progetto di Advanced Planning & Scheduling con l’obiettivo di allineare i tre layer organizzativi dell'azienda, Supply Chain, Commercial Offices e Manufacturing, e di gestire realtà produttive e organizzative molto diverse a livello globale.
In particolare la Direzione di Trelleborg Wheel Systems si era posta i seguenti obiettivi:
Non si trattava della semplice implementazione di uno schedulatore di produzione ma di un vero e proprio sistema di intelligence centrale in grado di gestire e tenere sotto controllo la produttività dei vari stabilimenti, considerando tutti i diversi vincoli produttivi world-wide.
Il progetto affidato a Tecnest ha in primo luogo coinvolto gli stabilimenti di produzione di Trelleborg Wheel Systems “solid-tires” e“agro-tires” dello Sri-Lanka.
Il modello pensato da Tecnest si basa sul concetto di “Digital Twins”: i “gemelli digitali” sono la copia perfetta di un prodotto manifatturiero o di un processo che interagiscono tra loro solo nel mondo digitale.
Il software FLEX è infatti stato usato per avere a livello della propria Central Supply Chain dei “gemelli” dei propri stabilimenti produttivi su cui verificare la fattibilità degli obiettivi di business.
[...]
I risultati sono stati concreti. «Il progetto è partito dallo stabilimento “solid tires” dello Sri Lanka, per il quale abbiamo ottenuto risultati tangibili sotto due punti di vista. Il primo è quello delle performance: in due anni i volumi di produzione sono aumentati del 15% e il livello di servizio al cliente in termini di on time delivery ha superato il 91%, mentre l’accuratezza delle previsioni è passata dal 79 al 90,1%», ha ricordato Filippo Setteceli, Vice President Supply Chain & Quality di Trelleborg Wheel Systems. «Il secondo aspetto è quello del vantaggio rappresentato dalla riduzione, pressoché immediata, dei giorni di lavoro del 3,6% in due anni». Sulla base degli ottimi risultati del pilota, il progetto è stato esteso anche allo stabilimento dedicato agli pneumatici del settore agricolo (light agro-tires) dello Sri Lanka.
«Anche in questo secondo caso abbiamo riscontrato un miglioramento della produttività di circa il 10% in due anni, e del servizio al cliente in termini di affidabilità delle date di consegna.
TECNEST S.r.l. - Reg. Imprese di Udine, C.F. e P.IVA 01534200306 - Iscr. C.C.I.A.A. - Udine R.E.A. 179349 - Cap. Soc. 31.200,00 Euro i.v.
© Multiways 2013 / Privacy policyCookie policy