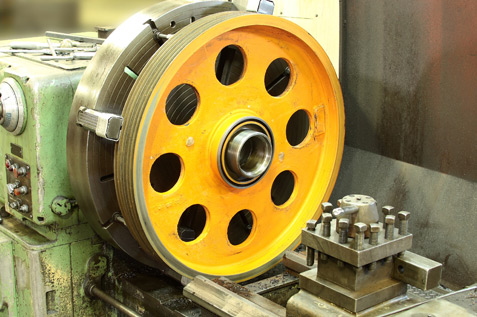
Where there is production, by definition there is also room to improve processes, first and foremost in terms of efficiency and performance. Where in the past the room for manoeuvre was dictated above all
by experience and the ability to analyse the individual situation, Industria 4.0 has the important merit of introducing procedural standards and being able to develop customised projects starting from a base of shared technologies.
The magazine HA Factory dedicated a nice article to the advanced planning and manufacturing execution project performed by Tecnest in CMA Macchine per Caffè, an Italian manufacturer of professional coffee machines based in Susegana (Treviso).
Un nuovo progetto APS e MES per Tecnest con Officine Forgiarini, azienda operante nel settore della progettazione e della costruzione di automazioni, movimentazioni industriali e prototipi.
Nello stabilimento di Castions di Strada (UD), Officine Forgiarini realizza anche macchine per la trasformazione di nastri abrasivi come smussatrici, presse e taglierine.
Il progetto prevede l'implementazione delle soluzioni FLEX APS e MES per la pianificazione e la schedulazione dei processi di produzione e la raccolta dati in fabbrica.
Visitare lo stabilimento di un cliente per toccare con mano i risultati dei propri progetti di ottimizzazione della produzione. Un'iniziativa che è ormai diventata una tradizione per Tecnest che quest'anno si è recata con tutti i collaboratori a Susegana (TV) per conoscere da vicino i processi produttivi e i miglioramenti ottenuti da CMA Macchine per Caffè, azienda specializzata nella produzione di macchine professionali per caffè espresso.
Per l’azienda titolare dei marchi Astoria e Wega, la gestione 4.0 dei processi portata dalle soluzioni di Tecnest ha migliorato efficienza e competitività: «Negli ultimi cinque anni i volumi sono aumentati di oltre il 36%, passando dalle 110 macchine prodotte al giorno a 150». Maurizio Gaio, responsabile dei sistemi informativi di CMA.
«Il mondo delle macchine per caffè non si ferma a un buon espresso: dietro a ogni tazzina non c’è solo tecnologia all’avanguardia unita a materie prime eccellenti, ma anche la capacità di rispondere alle richieste del mercato in termini di rapidità delle consegne, qualità e monitoraggio dei processi produttivi», ha proseguito Gaio. «Per mantenere il nostro vantaggio competitivo, da sempre l’azienda investe in tecnologia e innovazione, non solo sui prodotti ma anche sui processi. La collaborazione con Tecnest è cominciata nel 2007 e, negli anni, ha portato alla realizzazione di un progetto articolato che ha via via coinvolto e informatizzato tutti i principali processi operativi, dalla pianificazione e schedulazione della produzione al monitoraggio, raccolta dati, controllo qualità e tracciabilità in produzione”.
Tutto questo tenendo conto delle peculiarità e dei vincoli dei processi produttivi dell’azienda di Treviso, che opera prevalentemente con una logica “Assembly To Order” (assemblaggio dei componenti su commessa). «Ci siamo trovati davanti a due reparti principali – uno dedicato allo stampaggio di alcuni componenti e l’altro al montaggio del prodotto finito - che dovevano essere gestiti in modo sincronizzato per migliorare la precisione delle date di consegna. Questo in un contesto caratterizzato da un’elevata variabilità delle richieste e delle priorità in produzione, lotti medio-piccoli, numerose varianti di prodotto e vincoli produttivi dati dal numero finito di attrezzi e dalla complessità dei setup delle macchine di stampaggio”, ha ricordato Fabrizio Taboga, project manager Tecnest che ha gestito il progetto con CMA Macchine per Caffè, «Da tenere in considerazione, inoltre, la necessità di gestire specifici collaudi, controlli qualitativi e garantire la tracciabilità dei componenti critici, come valvole e caldaie, nel rispetto delle normative a cui è sottoposta l’azienda».
La soluzione è stata quella di implementare un sistema integrato di schedulazione e gestione della produzione che tenesse conto di tutti questi aspetti. «Il progetto che abbiamo realizzato in CMA ha visto l’introduzione delle soluzioni FLEX APS (Advanced Planning & Scheduling) per la schedulazione della produzione e FLEX MES (Manufacturing Execution System) per la raccolta dati e monitoraggio in tempo reale, la tracciabilità di prodotto e di processo con rilevazione dei materiali critici, la gestione dei collaudi e dei controlli qualità e l’analisi delle performance in produzione», ha spiegato Taboga. Il risultato ha avuto impatti notevoli in termini di crescita della competitività. Oltre all’aumento della produzione che dal 2012 a oggi ha portato da 24.000 a 33.000 le macchine per caffè in uscita da CMA ogni anno, il sistema ha migliorato anche la puntualità delle consegne. «Abbiamo ridotto i materiali mancanti e il lead-time di produzione è diminuito da quattro a tre settimane», ha confermato Gaio. «Oggi abbiamo una completa visibilità sulla produttività dei reparti, maggiore rapidità di controllo e di risposta in linea, maggiore correttezza dei dati e una tracciabilità completa del processo produttivo. In generale sono migliorate le performance produttive, eliminando gli sprechi e quindi riducendo i costi, in un’ottica di miglioramento continuo».
«L’industria 4.0 non è fatta di proclami, ma innovazione e soluzioni tecnologiche che hanno risvolti concreti nel manifatturiero», ha ricordato Fabio Pettarin, presidente di Tecnest che ha accompagnato i propri collaboratori in CMA. «Il toccare con mano i risultati raggiunti ci permette di rafforzare la nostra cultura aziendale. Condividere i contenuti di un progetto e conoscere da vicino i clienti sono attività fondamentali per rendere tutti i collaboratori partecipi del successo di un progetto.».
Dopo la presentazione del progetto e la visita ai reparti produttivi, i collaboratori di Tecnest hanno potuto visitare il moderno show room delle macchine per caffè Astoria e Wega. La giornata si è poi conclusa sui colli del Prosecco con una visita a una storica cantina e una cena in compagnia.
Un progetto di schedulazione della produzione e MES realizzato per migliorare la datazione degli ordini e ottimizzare il piano schedulato, ridurre i tempi di attrezzaggio delle macchine, reagire in tempo reale sui cambiamenti nell’area produttiva, migliorare l’efficienza dello stabilimento al cuore del processo produttivo di una delle più importanti aziende italiane nel settore della refrigerazione.
Rivacold è un'azienda specializzata nella costruzione di impianti e gruppi per la refrigerazione che si dividono in 3 principali linee di prodotto:
L'ampia gamma di prodotti si sviluppa in versioni standard e a disegno del cliente in diverse applicazioni dedicate ai seguenti mercati Ho.Re.Ca., vending GDO, agro-alimentare, medicale e farmaceutico.
Nell’ambito del processo produttivo di Rivacold costituisce un nodo centrale lo stabilimento chiamato “Rivacold 5”, dedicato alla produzione di pacchi batteria e componenti per le altre divisioni dell’azienda.
Tale stabilimento si trova al cuore del processo produttivo di Rivacold e risulta critico in particolare a causa delle macchine presenti (presse, saldatrici e mandrinatrici) che possono richiedere fino a un’ora di tempo per l’attrezzaggio.
A causa di questi lunghi tempi di attrezzaggio, lo stabilimento Rivacold 5 rappresentava un collo di bottiglia per l’intero processo produttivo. Lo stabilimento è suddiviso in due reparti, in uno di questi la fase che determina il ritmo produttivo e dà il battito alla produzione, è quella di pressatura, nell’altro la fase critica è la mandrinatura.
Inoltre il processo di programmazione e schedulazione della produzione gestito da Rivacold tramite l’MRP del gestionale AS400 ed Excel, presentava alcuni limiti. In particolare si riscontravano difficoltà nel definire una data precisa di consegna al cliente e nel fare valutazioni precise sul carico nel medio e nel breve periodo. Gli ordini stampati e rilasciati venivano sequenziati ed assegnati alle risorse dai capireparto con logiche di ottimizzazione delle macchine basate sull’esperienza, senza una visione globale degli ordini in essere.
Infine il processo di ripianificazione in caso di urgenze risultava molto dispendioso e non si aveva una visione precisa dello stato di avanzamento dei vari ordini.
Sulla base di queste considerazioni il management di Rivacold ha deciso di implementare una soluzione APS e MES con il supporto di Tecnest per migliorare i processi di schedulazione e avanzamento della produzione.
Con il progetto affidato a Tecnest, Rivacold si era posta l’obiettivo di migliorare il processo di datazione degli ordini e ottimizzare il piano schedulato al fine di rispettare il piano di consegna e minimizzare gli attrezzaggi.
L’introduzione di un sistema di Advanced Planning & Scheduling doveva aiutare ad automatizzare il processo di pianificazione di medio e lungo periodo, minimizzando le attività di modifica manuale del piano rilasciato e dare la possibilità di modificare il piano effettuando valutazioni simulative “what-if”.
Un’altra esigenza era quella di poter individuare per tempo le criticità produttive, in termini di mancato rispetto delle date di consegna al cliente, di variazione delle forniture (esterne o interne alla Rivacold) che costituiscono un vincolo per l’avvio delle attività e di variazione delle giacenze.
In reparto era inoltre importante avere a disposizione il piano schedulato in tempo reale, visualizzare disegni tecnici direttamente a bordo macchina, raccogliere i tempi consuntivati sulle risorse macchina e manodopera al fine di verificare l’efficienza e analizzare la bontà dei tempi preventivi e avere una visualizzazione in tempi rapidi dello stato di avanzamento dei singoli ordini produttivi
In una prima fase di progetto è stata fatta un’analisi dei processi di Rivacold 5, in particolare lo studio dell’albero delle risorse (macchine, gruppi macchina, centri di lavoro), la revisione dei cicliper fornire allo schedulatore dati che replicassero in modo fedele il processo produttivo e la formalizzazione dei vincoli di processo (matrici di set-up).
Nel gestire il processo di schedulazione in Rivacold 5 ci si è concentrati sull’ottimizzazione delle fasi critiche che determinano il ritmo produttivo nei due diversi reparti. In un caso la fase critica è quella di pressatura, nell’altro è la fase di mandrinatura.
[...]
TECNEST S.r.l. - Reg. Imprese di Udine, C.F. e P.IVA 01534200306 - Iscr. C.C.I.A.A. - Udine R.E.A. 179349 - Cap. Soc. 31.200,00 Euro i.v.
© Multiways 2013 / Privacy policyCookie policy