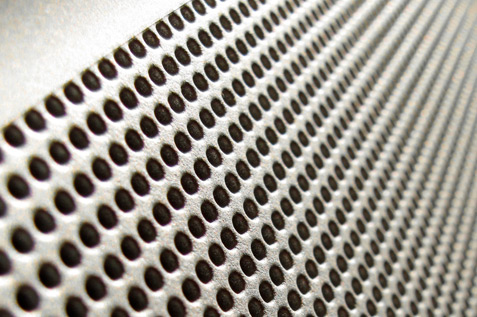
Una soluzione di pianificazione e gestione dei processi di produzione tenendo conto dei vincoli legati, non solo alla disponibilità di materiali e attrezzature, ma anche alle competenze degli specialisti, che ha permesso di avere una completa visibilità su processi e risorse, migliorare l’affidabilità delle date di consegna, ridurre del 30% i tempi per la creazione del piano di produzione e migliorare l’efficienza globale.
DMM Spa è un’azienda marchigiana specializzata nella lavorazione del metallo per la realizzazione di rivestimenti su misura e finiture innovative per diversi settori di mercato, dall’arredamento all’edilizia.
I prodotti DMM sono unici nel loro genere in quanto sono progettati, a volte anche a partire da un semplice schizzo su carta, dai progettisti dell’ufficio tecnico assieme al clientee agli architetti coinvolti.
Un'altra caratteristica distintiva della DMM è la capacità di studiare e realizzare finiture speciali per dare al metallo effetti cromatici o texture particolari. La particolarità di queste finiture è che possono essere eseguite solo manualmente da personale specializzato.
Lavorando su commessa e realizzando componenti e prodotti su misura – dai piani di lavoro ai restauri delle chiese - lafase di progettazione è per DMM una fase importante ma anche delicata e dispendiosa in termini di tempo.
Prima del progetto realizzato con Tecnest, il processo di pianificazione delle risorse in DMM veniva eseguito manualmente attraverso riunioni con i responsabili dei reparto e risultava quindi un’attività lunga e complessa. Inoltre, non avendo visibilità sulla situazione in reparto e sugli ordini di produzione, vi era una scarsa percezione del carico di lavoro con una conseguente difficoltà a rispettare le date di consegna. Era inoltre difficile gestire eventuali eccezioni ricalcolando al volo il piano e avere sotto controllo la disponibilità dei materiali a giacenza.
Gli obiettivi del progetto affidato a Tecnest da DMM, erano in primo luogo, ridurre i tempi per la creazione del piano di produzione, tenendo conto dei vincoli legati alle competenze degli specialisti in fabbrica, migliorare la precisione delle date di consegna, gestire in modo dinamicole variazioni nei piani di produzione e i materiali mancanti.
Era inoltre importante migliorare la precisione dei dati a disposizione dell’azienda e la possibilità di analisi e controllo delle performance.
In ambito Execution, invece, vi era la necessità di avere una maggiore visibilità sui dati di produzione (consuntivi, presenze, prelievi a magazzino) e di monitorare lo stato di avanzamento della produzione.
In una prima fase è stato portato avanti un dettagliato lavoro di analisi e mappatura delle competenze necessarie per lo svolgimento delle diverse attività in ciascuna fase di produzione. E' stata creata una matrice di competenze che associa a ciascuna persona uno o più skill tra quelli mappati e il relativo livello di conoscenza/esperienza (base, medio, elevato).
Successivamente si è passati all’implementazione e configurazione delle soluzioni software J-Flex APS e MES. L’obiettivo era quello di introdurre un sistema integrato che gestisse tutti i processi di produzione, a cominciare dall’ordine di vendita, passando per la gestione dei materiali, alla pianificazione e schedulazione della produzione, fino alla fase del controllo e avanzamento in reparto.
Una soluzione MES che guida l’operatore nell’attività di avanzamento e consuntivazione sulla linea dedicata alla produzione di unità condensatrici di Rivacold. Un sistema completo di funzionalità per il monitoraggio e tracciabilità completa per ogni singola matricola al fine di risalire facilmente a eventuali difetti o problematiche in produzione.
Rivacold è un'azienda leader nella costruzione di impianti e gruppi per la refrigerazione che si dividono in 3 principali linee di prodotto:
L'ampia gamma di prodotti si sviluppa in versioni standard e a disegno del cliente in diverse applicazioni dedicate ai seguenti mercati Ho.Re.Ca., vending GDO, agro-alimentare, medicale e farmaceutico. Rivacold è oggi un gruppo con 7 divisioni, 5 filiali a livello internazionale e una rete capillare di vendita sia in ambito nazionale che internazionale.
Nel 2014 Rivacold ha costruito una nuova linea esclusivamente dedicata alla produzione di unità condensatrici per un suo specifico cliente. Il layout della linea è stato studiato in modo tale che fosse pensata come una linea a flusso teso con logica FIFO, in cui i tempi sono bilanciati nelle varie fasi. Le fasi di produzione sulla linea sono: prelievo dei materiali e componenti da assemblare (picking), assemblaggio componenti, assemblaggio del compressore, test, cablaggio e collaudo funzionale, imballaggio.
Generalmente il flusso prevede la presenza di una persona per ogni fase, solo in alcuni casi la stessa persona lavora su due fasi contemporaneamente. Le date di consegna, definite dal cliente, sono tassative, mentre il lead time di produzione è di circa 15-20 minuti. I lotti sono generalmente piccoli è possono variare dai 2 agli 80/100 pezzi.
Per garantire la massima visibilità e il miglior servizio al cliente finale, Rivacold aveva l’esigenza di dotare questa linea di un sistema MES per tenere sotto controllo le fasi di produzione, fornendo una guida proattiva agli utenti nell’esecuzione dei diversi step e che allo stesso tempo raccogliesse i dati e garantisse la massima tracciabilità dei componenti, ordini, prodotti finiti, macchine e operatori coinvolti.
Sulla base delle esigenze e degli obiettivi definiti, è stato implementato il sistema J-Flex MES con l’applicativo client JET per la raccolta dati e consuntivazione in reparto.
Gli ordini di produzione vengono datati dall’MRP del gestionale e acquisiti in J-Flex che effettua una sequenziazione delle attività sulla base di specifici parametri e vincoli. Tale sequenziazione dà luogo a una worklist che approvvigiona la fase di picking dei materiali. Gli ordini di produzione da eseguire vengono infatti visualizzati sul monitor JET a bordo macchina con la rispettiva sequenza dei materiali che devono essere prelevati. Gli operatori possono quindi effettuare le dichiarazioni di ingresso/uscita, di inizio e fine lavorazione e di completamento della fase di picking dei materiali, trasversale a tutte le linee.
Una volta completata questa fase di picking, si inizia con la produzione vera e propria sulla linea. Il sistema MES guida l’operatore nelle diverse attività lungo le fasi del processo produttivo attraverso una sequenza operativa molto semplice, e allo stesso tempo crea i legami di tracciabilità tra le diverse entità coinvolte. (...)
Il sistema J-Flex MES gestisce l’avanzamento in tempo reale sulle varie fasi e il calcolo di tempi e dell’efficienza in produzione. Per ogni ora, viene definito un target produttivo (es. 16 pezzi) e, allo stesso tempo, viene segnato dagli operatori il numero reale di pezzi prodotti. In questo modo è possibile calcolare l’efficienza in termini di pezzi prodotti su pezzi previsti.
Tali dati e indicatori di efficienza sulla linea sono riportati in forma grafica e riassuntiva all’interno di una dashboard role-based di J-Flex a disposizione del responsabile.
II sistema MES implementato sulla linea di Rivacold gestisce la raccolta dati, controllo, avanzamento nelle diverse fasi del processo di produzione e garantisce la tracciabilità di ogni singola matricola e la rintracciabilità completa di prodotto e processo in caso di difetti.
Questo ha portato a una drastica riduzione di difetti e errori nella gestione delle attività in produzione dovuta anche allo studio e implementazione di una procedura guidata che segnala automaticamente sul sistema eventuali errori nelle dichiarazioni da parte degli operatori.
Il management di Rivacold ha oggi visibilità su tutti i processi, sulle attività svolte e sui legami tra i componenti utilizzati nel processo produttivo e ha a disposizione informazioni e dati per il monitoraggio e il calcolo dell’efficienza della linea.
Formest, azienda di Saonara (PD) specializzata nella lavorazione lamiera e nelle costruzioni meccaniche di alta qualità e tecnologia per diversi settori di applicazione, ha scelto la suite J-Flex per gestire tutte le operations in modo integrato e completo.
Negli ultimi anni Formest ha conosciuto una forte crescita, affermando la sua posizione di leader nel settore della progettazione e della lavorazione della lamiera per grandi commesse. In particolare l'azienda realizza carterature complete e protezioni per macchine utensili, strutture ed involucri per la industria alimentare, ausilii, accessori e componenti per l’industria medicale e l’estetica medica.
Formest offre ai propri clienti un servizio completo e specialistico, dalla progettazione alla realizzazione di tutte le lavorazioni (carpenteria, taglio laser, piegatura, calandratura, saldatura, fresatura, ecc.), fino all'installazione del prodotto finito.
Nell'ambito di un processo di revisione e innovazione dei propri processi e delle proprie infrastrutture aziendali, il management di Formest ha manifestato l'esigenza di introdurre una soluzione integrata, tecnologica e performante per gestire tutti i processi logistico-produttivi dell'azienda, in particolare quelli relativi alla produzione di manufatti in lamiera e alla gestione di commesse caratterizzate da bassa numerosità ma notevole complessità di cicli e distinte.
Dopo un'attenta software selection, è stata scelta la suite software J-Flex a copertura dei processi di Configurazione Tecnico-Commerciale, Preventivazione ed Offertazione, Vendite, Acquisti, Conto Lavoro, Gestione del Magazzino (WMS), Pianificazione e Sequenziazione, MES e gestione della qualità in Produzione.
Il nuovo progetto affidato a Tecnest prevede infatti l'implementazione delle soluzioni J-Flex APS per la Pianificazione dei Materiali e delle Attività di Reparto, J-Flex MES per la gestione e monitoraggio dell'esecuzione delle commesse in fabbrica e J-Flex OPM per la gestione dei processi di ciclo attivo e ciclo passivo, comprensiva del configuratore tecnico-commerciale per la gestione dell'offertazione di commessa. Il software J-Flex verrà interfacciato con i sistemi amministrativo-contabile, PDM e di Nesting presenti in azienda per una gestione integrata e completa dei dati aziendali.
Leggi le nostre referenze nel tuo settore di riferimento e scarica i nostri case history!
Tecnest e le soluzioni J-Flex di Pianificazione, Schedulazione, Sales Forecasting, Controllo e Monitoraggio della Produzione sono state scelte da DMM S.p.A. per supportare il processo logistico - produttivo presso il sito produttivo di Montecalvo in Foglia (PU).
DMM S.p.A., con più di 40 anni di esperienza nella lavorazione dei metalli, è leader nazionale ed internazionale nella fornitura di prodotti in metallo e/o composti e servizi di progettazione e consulenza creativa in particolare nel campo dell'arredamento e dell'edilizia.
TECNEST S.r.l. - Reg. Imprese di Udine, C.F. e P.IVA 01534200306 - Iscr. C.C.I.A.A. - Udine R.E.A. 179349 - Cap. Soc. 31.200,00 Euro i.v.
© Multiways 2013 / Privacy policyCookie policy