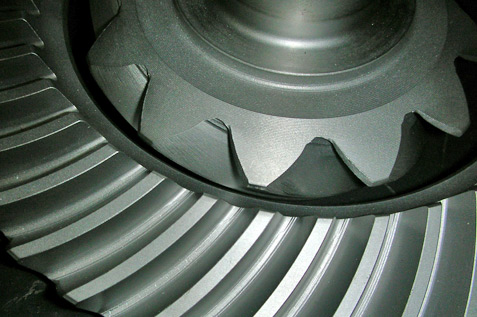
Un'unica centrale di comando operativa, sottoforma di software per quattro bracci armati della produzione in ambito meccanica di precisione per l’automotive. Il progetto della veneta TFM Group, azienda da 64 milioni di euro di fatturato ed oltre 600 dipendenti, guarda ad un futuro interamente digitale per fabbriche interconnesse e sostenibili.
Integrare, interconnettere e digitalizzare su più stabilimenti per avere maggior visibilità sull’avanzamento e sui costi della produzione in fabbrica, raccogliendo tutti i dati su un’unica piattaforma integrata con il gestionale aziendale.
Una logica “single brain” per aumentare il controllo e la visibilità sulla produzione garantendo gli altissimi standard qualitativi richiesti dal mercato dell’automotive e la competitività addentrandosi – per davvero - nella Digital Transformation.
Così TFM Group, azienda di Padova, con stabilimenti in Italia, in Repubblica Ceca e Romania, specializzata principalmente nella produzione di componenti meccanici lavorati ad alta precisione per diversi settori (Automotive, Bike, biomedicale etc.), raccoglie la sfida – e più che di transformation, si parla di revolution - con un progetto a lungo termine che coinvolge gli stabilimenti produttivi italiani di TFM e della consociata Spiral su più livelli.
Il progetto, avviato nel 2022, ha già visto nascere il primo step con l’interconnessione delle macchine produttive in logica 4.0.
Un progetto che guarda alla produzione in ottica strategica partendo dalla pianificazione della produzione arrivando agli stabilimenti, asservendo la tecnologia agli obiettivi di business, al processo decisionale ed alle sfide presenti e future.
“Un progetto completo - raccontano dalla Tecnest - I dati si trasformano in informazioni, le informazioni in valore. Così raccogliamo il concetto di Data Lake, riuscendo ad attingere in ottica strategica a tali dati da ogni stabilimento, grazie all’applicativo, rendendoli importanti informazioni di business. Così la produzione non è più solo digitale, ma “intelligente”: pianificazione esatta e simulativa per garantire tempi di consegna competitivi, tracciabilità interna di prodotto e dati di avanzamento sulla produzione per assicurare gli altissimi standard qualitativi richiesti dal mercato di riferimento”.
Così l’ottica multiplant si trasforma da complessità a risorsa.
“Stiamo rivoluzionando il nostro modo di produrre - racconta Michele Celi, IT Manager del gruppo - Parole d’ordine per il progetto che è ancora work in progress sono: visibilità, integrazione e controllo sui costi. Le sfide sono tante: dallo shortage delle materie prime, all’energia. Oggi digitalizzare è diventato imprescindibile per produrre in modo efficiente e sostenibile”.
“Lavoriamo in un settore in grande trasformazione e fermento – dichiara l’AD del gruppo Giorgio Bertolina - Parliamo di componentistica per il motore a scoppio – un business il cui riposizionamento è già cominciato da anni e per il quale la parola d’ordine è oggi flessibilità. Gli investimenti vanno quindi nella direzione di una struttura digitale che sappia supportare ed amplificare questa flessibilità. Sono state tante le sfide degli ultimi anni. Non ultima quella dell’aumento dei costi energetici alla quale risponderemo con la realizzazione di un parco fotovoltaico installato sul tetto del nostro stabilimento di Reschigliano. Ma il problema non è chiaramente solo di costo: strumenti e strategia ci porteranno a rispondere ai requisiti di sostenibilità che un’azienda che guarda al futuro deve considerare parte integrante del proprio sviluppo”.
FCF Fontanafredda Cold Forging srl, nota azienda del Friuli Venezia Giulia, attiva nel campo della tecnologia per lo stampaggio a freddo per il settore Automotive, ha scelto la soluzione Flex-MES con interconnessione macchine per potenziare il proprio comparto produttivo.
L’azienda, che lavora per alcuni dei più importanti brand internazionali del settore Automotive, con logica produttiva MTO (Make to Order), forte dell’esperienza ultradecennale e dei suoi numerosi collaboratori, si è rivolta a Tecnest con l’obiettivo di garantire precise e rapide date di consegna al cliente finale. FCF Fontanafredda Cold Forging è infatti pronta a sostenere a pieno ritmo la ripresa del settore nel post-pandemia, assicurando sempre la massima qualità a livello di servizio.
L’interconnessione delle macchine, in chiave Industry 4.0, inoltre, garantirà la comunicazione bidirezionale assicurando all’azienda la lettura di dati di produzione sempre aggiornati.
TECNEST S.r.l. - Reg. Imprese di Udine, C.F. e P.IVA 01534200306 - Iscr. C.C.I.A.A. - Udine R.E.A. 179349 - Cap. Soc. 31.200,00 Euro i.v.
© Multiways 2013 / Privacy policyCookie policy